All engineers tend to optimize their steel structure designs to at least some point because the cost is directly related to volume. Typically, material costs go hand in hand with the volume. As very likely manufacturing, logistics and assembly costs also. Its obvious that weight can be optimized with more sophisticated analysis methods, but also choosing right steel grade for the application may be excellent idea.
When selecting stainless steel materials, it’s crucial to consider factors such as corrosion resistance, strength, and cost. Stainless steels are categorized into different grades with unique properties best for specific applications. For instance, austenitic stainless steel like 316 is well known for its excellent corrosion resistance and formability, making it ideal for environments exposed to moisture and chemicals. On the other hand, duplex stainless steels offer excellent strength and ductility combined with awesome corrosion resistance. That’s makes them number one choice for demanding structural applications such as bridges.
For example, applications where moderate corrosion resistance is needed, initial material proposition might be 316L (EN 1.4404) with PRE number 24. But I would rather pick lean duplex grade 1.4162 with similar corrosion resistance (PRE 26) and with more than double the design strength (480 vs. 220 MPa)!
Rectangular hollow sections have various applications in steel structures. Trusses, columns, diagonal beams and short to medium span horizontal beams, just to mention few. And as we know, some types of structures don’t benefit much from higher steel strength. For example, if deflection limit state is critical, higher steel strength wont make much.
But vice versa, there is also many structures ideal for cherry picking. Such as tension members or non slender compression members!
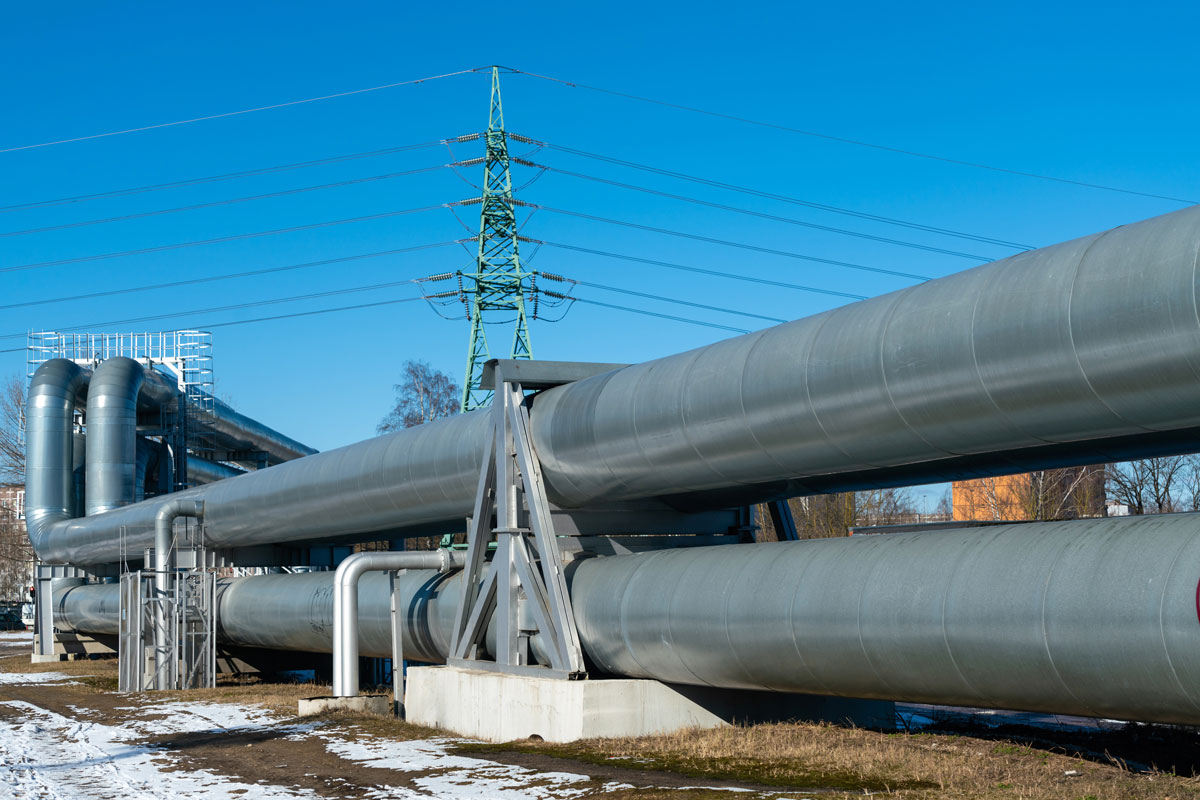
Or another easy example is structure with short spans or deflection limits not critical.
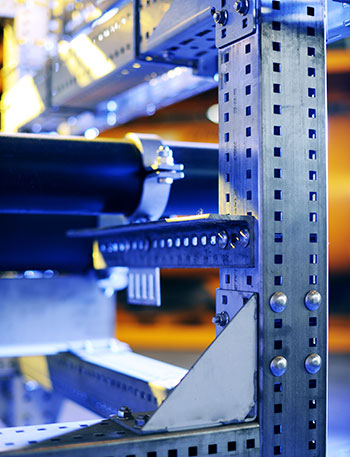
In these kinds of applications, the weight saving potential may be up to -50 % when comparing Lean Duplex stainless steel grades to traditional austenitic grades. With that huge difference in structural weight, its very likely to achieve direct cost savings.
And what is very important, every kg not consumed in steel structure equals around 1,7 kg (depending on product) less CO2 in atmosphere!
The writer
Tommi Purtilo
Business Development ManagerEnergy Industry, Hollow sections & profilesStalatube Oy (Finland)
Technical support