Special attention paid to preventive action
Promoting a safety culture based on volunteering and community spirit. We encourage employees to be bold in their observations and initiatives. The aim is for everyone to care about their own safety and that of their colleagues. We don’t blame others, we want to make sure everyone stays healthy and safe.
At Stalatube, we have reached a significant milestone: two whole calendar years without a single workplace accident resulting in sickness absence. This achievement is the result of long-term work to improve our safety culture and develop preventive action.
The reporting of near misses and safety findings is an essential part of the safety culture. Recording these incidents helps to identify and eliminate risks before they lead to actual accidents. In 2024, the number of observations more than tripled year-on-year. This shows that our employees are becoming more active in making safety observations.
Preventive action is key to improving safety at work. Safety observations are important because they help to eliminate risks before accidents occur. In early 2024, we launched an internal safety campaign to encourage staff to make observations and report near misses with a low threshold. At the same time, a new, more user-friendly and mobile-friendly system, Falcony, was introduced. The campaign and the new system have lowered the threshold for making observations and made people think more actively about safety.
The quality of safety observations has also improved significantly
We are now getting very high-quality observations, and the observations are based on voluntary work. However, we have found that quality pays for quantity,” says Teppo Lassila, who is responsible for safety at Stalatube.
Every employee’s contribution is important. An observation made can be a small thing that does not require a significant investment. Nor does the whistleblower have to solve the problem himself; simply filing a report is enough. Significant improvements have been made to the working environment through safety findings and initiatives. For example, the tying of gas cylinders, the location of fire extinguishers and the contents of first aid cabinets have now been checked more regularly. Other findings have also led to significant investments, such as the replacement of a welding gas suction system and the purchase of smaller coils, but Stalatube does not put a price on safety.
The measurement of proactive safety at work is constantly being developed. In the future, the aim is to measure the number of hours spent on preventive activities. The number of absences due to illness has remained low, and employees’ well-being is actively supported. Psychosocial and cognitive stress has been selected as a priority area and support services have been developed accordingly.
Developing a safety culture is an ongoing process in which everyone’s contribution is important. Together, we can ensure that our workplace remains safe and healthy for everyone.
Safety initiatives are also rewarded. One example of a rewarded safety initiative is the operator-designed oil through on the production line to prevent oil spillage on the floor. We believe that our reward system also contributes to encouraging employees to make observations and take initiatives.
The trend is good, and we have made progress in our proactive work over the past year,” says Teppo.
Even a small thing can pose a big safety risk. Laura Neuvonen, our Purchasing Assistant, has to climb a ladder to label heavy mother coils. After making a safety observation, Laura was fitted with a sturdier and safer ladder.
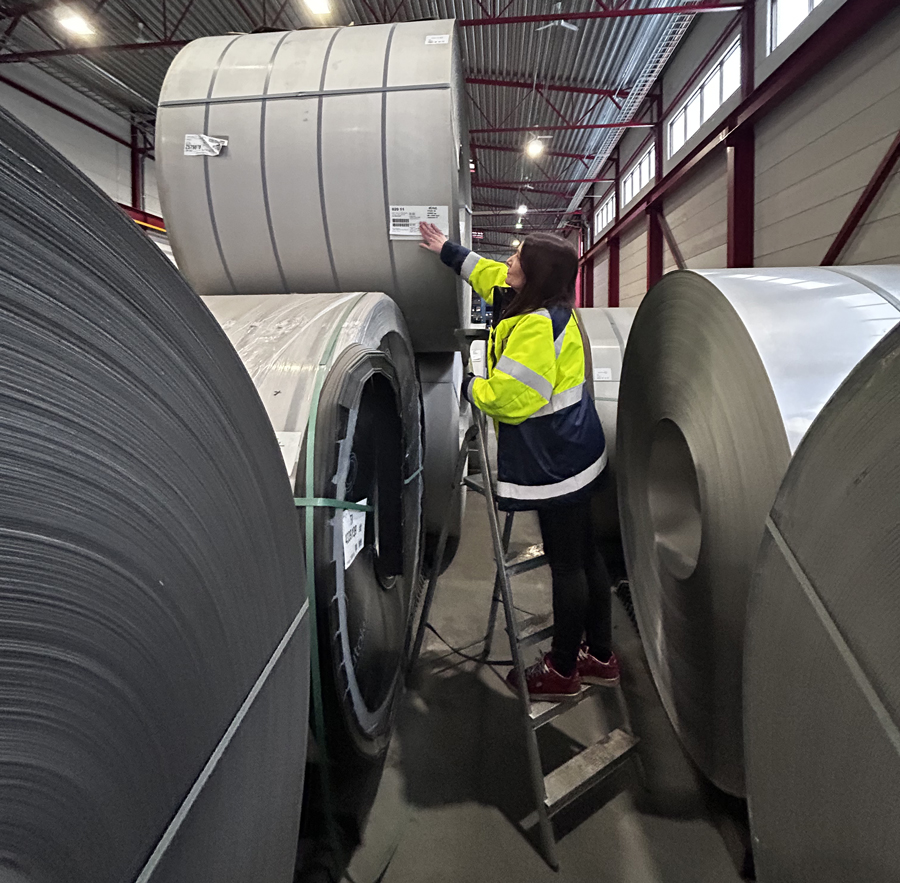