Over the years, we have taken several preventive measures to improve occupational safety. Some ten years ago it was not unusual that people wore shorts and sandals when working in our plants. Today, occupational safety is one of the key elements in our company’s management. At first, personnel might have felt that the measures improving occupational safety were forced upon them, and some changes were even opposed by our employees, but today, these measures are taken for granted. Of course, this kind of cultural change did not happen overnight. We have created our new culture of occupational safety one step at a time and involved our personnel in the process.
“Now, no one would even think about welding while wearing sweatpants, it is completely out of the question. All the small changes have gradually transformed the company culture as a whole,” says Occupational Safety and Health Representative Aarni Lyhty, who has worked as an operator at Stalatube for more than 20 years.
5S project
The overall order and cleanliness of the plant has a great impact on occupational safety. In 2011, we started a 5S project aimed to enhance productivity and improve the order and cleanliness of our plants. The focus of the project was to clear the plant of all items that do not belong there, to clean the floors and to take measures to prevent oil from leaking onto the floors and passageways, for example, significantly reducing the risk of slips. In addition, the project included creating solutions to reduce the amount of dust in the air inside the plant. The project proceeded from one machine to another, and after it was completed, the plant has been a much safer place to work and maintaining the cleanliness level is now easier and it feels more meaningful.
“Even a steel company can be clean if it wants to be,” says Production Director Tuukka Juhanila.
Machine safety is planned together with employees
The first efforts to improve machine safety were made already back in 2012 when a risk assessment was ordered from an external operator for the first time. Since then, significant changes to machine safety have been implemented. Stalatube’s Development and Project Manager Ari Sarajärvi can provide several examples of this.
“Welding protection has been improved with fiber laser projects. When using this method, the demands are much higher than with other methods. In the past two years, the HF line has seen several improvements in safety, such as improving the safety of the shaping stage and adding local application systems, and the safety mechanisms at the end of the line have been improved to meet the current demands,” Sarajärvi says.
Ari knows what he is talking about, as he has more than 10 years of experience in occupational safety matters.
“Currently, we are looking into the safety aspects of manufacturing particularly long hollow sections,” Sarajärvi continues.
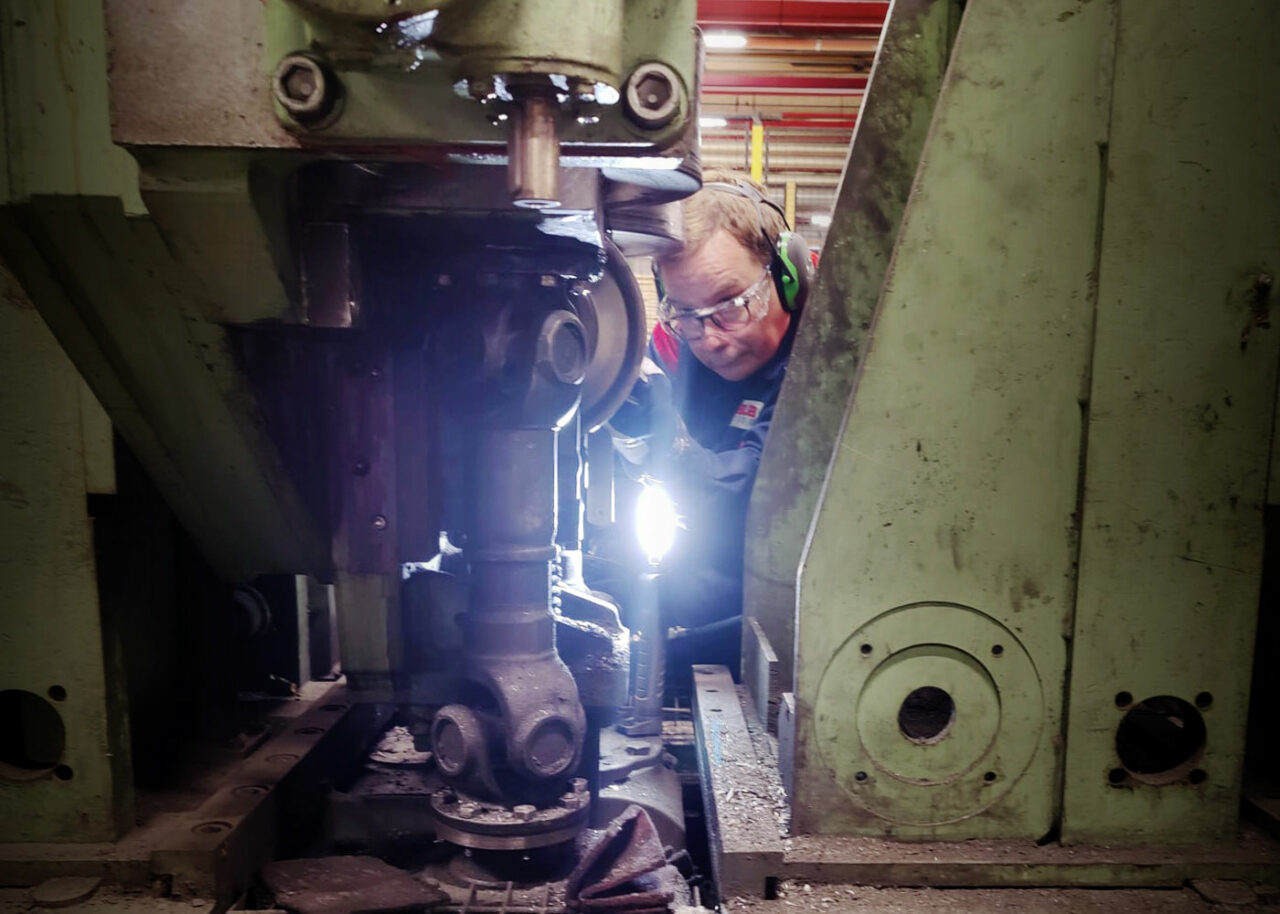
Planning together for the best result
Many work stages require employees to be particularly careful. For example, moving mother coils weighing as much as twenty cars or lifting tube bundles requires great caution. Functional and appropriate work clothes are a basic requirement at Stalatube today. Special attention is paid to the fire safety of work clothes. In outdoor clothes, high-visibility colors and reflectors are another particular focus. The plant area is off-limits without appropriate safety shoes, safety goggles, and hearing protection.
“Safety goggles have saved more than one eye in the past few years, so we have concrete evidence to show how important it is to follow the guidelines,” Lyhty says.
Even though occupational safety is at the core of everything, safety arrangements must not make anyone’s work more difficult. Therefore, it is important to involve the personnel in planning and making the arrangements. Safety matters are regularly discussed in line meetings and in general briefings. When occupational safety guidelines and general carefulness are discussed often and thoroughly, people remember and follow them better.
Well-being at work contributes to occupational safety
Tiredness often leads to carelessness, which increases risks at work. Stalatube has participated in the “Kevennä kuormitusta” (“Lighten the load”) project by the Centre for Occupational Safety. The project’s goal is to draw attention to how employees cope at work. In recent years, the scope of occupational safety has broadened to include well-being at work as well. For the time being, taking care of employees’ well-being at work is largely voluntary for employers, as there are no laws or standards regarding this aspect, in contrast to occupational safety.
“The wellness day organized in Pajulahti last year is one example of this kind of activity. It is a significant financial input from the employer, because it means that the entire personnel is out of office for the day, no products are finished and no deliveries are made,” says Lyhty.
Stalatube supports the physical and mental well-being of its personnel in many ways. Our offering allows each employee to find a way to take care of themselves in the best way, either individually or together with coworkers.
Increased productivity through improved safety
Stalatube is certified according to the ISO 45001 standard on occupational safety and health. We have also implemented the new Falcony system where everyone is required to report all near-accidents and record all work accidents in detail. Occupational safety is developed in cooperation with authorities through occupational safety and health inspections and occupational health examinations as well as workplace surveys, for example. Stalatube also has its own occupational safety and health committee which assesses the safety conditions internally. Even though the root cause for this change is the new, more strict legislation and the requirements are set by law and standards, improved occupational safety also directly affects the bottom line.
In automated operations, safety improvements have also led to significant improvements in productivity. Output is increased when the production can continue without interruptions.
Advances in technology also create new, safer working conditions. For example, the plant’s new lighting is not only efficient in lighting up the otherwise grey factory premises but it is also more energy-efficient and thus more cost-effective.
“Investing in safe working conditions does not reduce productivity, quite the opposite,” says Juhanila.
Research shows that preventive measures promoting well-being at work also affect the company’s bottom line.
“Our indicators also show that employee satisfaction as well as productivity in manufacturing have both improved, while the number of absences has dropped. The guiding principle is that all employees have the right to go home healthy and happy,” Juhanila says.