Carefully prepared is nearly finished. With this principle, TUTEKA manufactures all kinds of special structures and furnishings with uncompromising workmanship and long-standing experience in its workshop in Turku.
TUTEKA’s story goes way back. The company is run already by the third generation of the Kiviniemi family. The company’s turnover is nearly MEUR 3.5 and it employs more than 20 employees. Fixtures and furnishings designed and manufactured by the company established by Aake Kiviniemi in 1946 can be found all over the world. The Turku-based company’s designer furnishings, staircases, and handrails are featured in both grand cruise ships and luxury hotel chains. The common denominator between TUTEKA and Stalatube is stainless steel, which is both an aesthetically impressive and durable construction material.
TUTEKA and Stalatube share a long history. Already in the 1970s, the great entrepreneurs of their time, Aake Kiviniemi and Reino Rajamäki, founder of Stala, entered into cooperation which has only intensified over the course of years. Customers are provided with not only structural hollow sections but also the expertise of Stalatube’s employees.
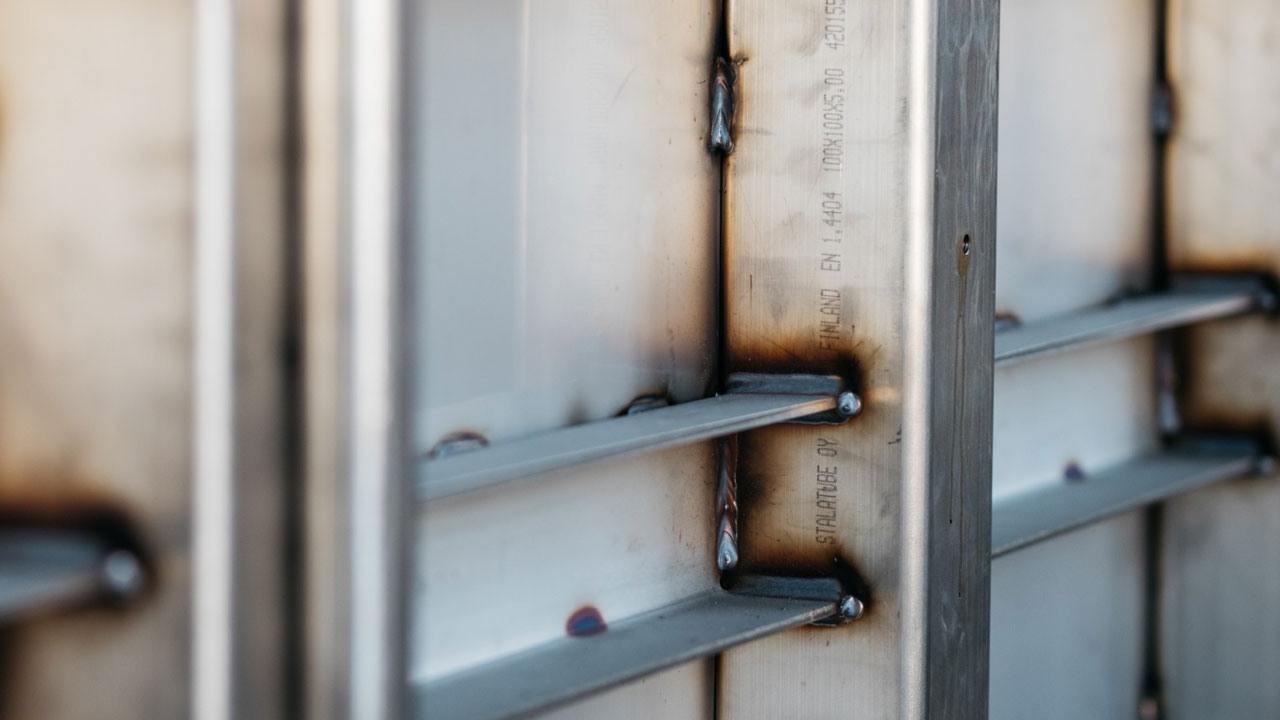
Jukka Matilainen
“With Stalatube, everything works both ways. As a customer of Stalatube, I’m provided with not only high-class stainless steel tubes but also the expertise and know-how of our contact persons. I place immeasurable value on the fact that we can work together to come up with solutions to achieve an optimal outcome,” says Aleksi Kiviniemi, CEO of TUTEKA
The network of requirements is wide, delays are not tolerated
Construction projects often involve many different operators who are all responsible for their own contribution to the big picture. Each construction stage proceeds in a carefully planned order. If one contractor’s schedule fails, it interferes with the work of all the other operators and, in the worst-case scenario, the completion of the entire project. The schedule is often tight and planned in detail. Delays are not tolerated or they carry a hefty price tag. Therefore, it is particularly important that the subcontractors’ delivery schedules are not compromised either.
“Stalatube’s delivery times are reliable. This has been one of the cornerstones of our cooperation. When something has been agreed on, it will be done. Smooth communication between Stalatube and TUTEKA is also important to ensure that both parties are on the same page about the progress of the project,” says Kiviniemi.
In large-scale projects, the network of requirements from various operators is wide. Matters to be taken into account include technology, lighting, electricity, architect’s wishes, and the requirements of several other operators. The network of requirements is large and extends far and wide. That is why it is important to be able to trust that your own chain of partners will not let you down.
150 meters of the stainless tube for a pool
When splashing around in a swimming pool, one rarely thinks about what it actually takes to build one. The latest pool project of TUTEKA was carried out at a demanding special site located in Southern Finland. The rectangular pool with a depth of two meters has a capacity of 50 cubic meters of water. The structure and its supporting beams must meet particularly strict requirements. Although this was not our first joint swimming pool project, over 300 hours of work were used solely to plan this pool.
“Chlorine and other chemicals used in swimming pools are corrosive, which means that even stainless steel must withstand demanding conditions. The material used in this project was acid-resistant 316L (EN 1.4404). The aesthetic quality of the material is also an important factor in similar sites to ensure that no signs of corrosion, including spot corrosion, appear over the course of time,” says Lari Brask, Director of Product Development and Technology at Stalatube
All the necessary preparations for the pool were carried out in TUTEKA’s workshop and its partners’ facilities. Careful preparations ensured that the pool met all the requirements precisely. The durability of Stalatube’s products, i.e. the yield strengths of structural hollow sections, is a crucial factor in calculations. In addition to durability, the total weight of the structure is also central.
“In the manufacturing stage, we also have to think about how the project should be carried out, as manufacturing the structures and completing them as far as possible in the workshop facilitates and speeds up on-site installation work. Our strength is that we make all the preparations in the workshop, which leaves only the installation work to be carried out at the actual site,” says Kiviniemi.
The careful preparation process also includes logistics planning. Even large structures manufactured and nearly completed in the workshop often have to be transported to a partner’s facility for processing during the preparation stage. This was also done in the swimming pool project in question. After the actual construction stage, the swimming pool was test filled, measured, emptied and immersed in a beck for acidifying before it was finally transported to the site.
Another similar pool, built-in collaboration with Stalatube, ended up in Saudi Arabia, in the resort-type destination, making the pool’s weight, rigidity, portability, and degree of prefabrication even more important.
Significant savings thanks to the total weight of the structure
The more the total weight of the structure can be reduced with the right material choices, the easier the product is to prepare and transport from one place to another at different stages of production. A reduced total weight saves costs as less material is needed. On top of this, the carbon footprint of the project is reduced due to savings on material and transport costs.
In the pool project, the weight of the completed structure was actually lower than the target set by the construction designer, thanks to Stalatube’s structural hollow sections and experts’ weight calculations. With the help of experts, significant weight and total cost savings can be achieved, particularly with regard to large hollow sections.
“We Finns know what we’re doing. We work fastidiously and with great ambition. It’s all about uncompromising cooperation that is founded on the premise that only the best and optimal solution is good enough. Together we want to be the best in the world,” Kiviniemi sums up.
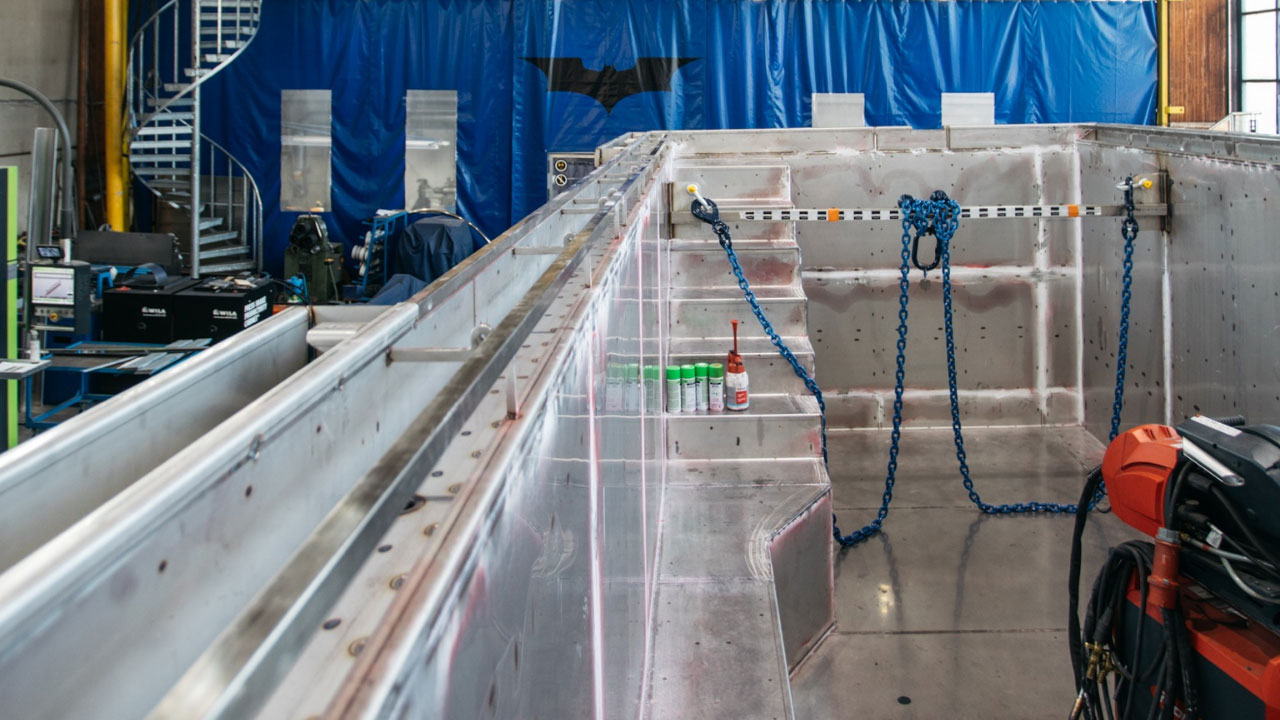
Turun Teräskaluste Oy is a family business founded in 1946. It manufactures fixtures, furnishings, and special structures including staircases, handrails, and other custom-made interior decoration elements for luxury sites, such as cruisers, superyachts, hotels, and other public spaces across the world. In addition to steel and non-ferrous metals, the company uses stone, wood, and glass materials in production.
The keywords of TUTEKA’s production are prefabrication and modularization: all products are manufactured and finished in their own workshop in Turku and delivered to the site ready for installation. Thanks to its expert design department, the company’s greatest strengths lie in challenging projects that require in-depth experience. For more information, visit www.tuteka.fi